When ID Follows You Home at Night
I chose a career in industrial design and consulting because of the diversity it offered. Industrial design merges many different skills and disciplines to create products that solve user problems, provide functionality and are aesthetically pleasing. To some extent, an industrial designer needs to be a jack of all trades. Drawing, sculpting, building, engineering and problem solving are but a few of the skills required to be a good industrial designer. When I was a kid, these were the things that I did for fun. My dad always told me that you had to love what you did for a living, and I really took that to heart when adopting my chosen profession. Working as an industrial designer for the past 20 years, I often found myself putting things like drawing and sculpting aside after work. We all have hobbies and things we do when we go home to get away from the daily grind. When you have kids, those hobbies often take a backseat in order to make time for their interests.
Recently, my son, an avid guitar player, saw a homemade guitar. He liked it so much, he asked me if I thought it was a project we could do. I saw this as a great opportunity to bring our hobbies together for the ultimate bonding experience. When building a guitar, there are several approaches that one could take: From purchasing off the shelf parts; body neck, electronics and hardware for a simple “home built” electric guitar, all the way to bending plywood and winding your own pickups. As a designer, just assembling off the shelf parts didn’t sit right, it seemed like a cop out. No one would even notice that you built it unless you told them. We wanted something that would stand out on stage and make people ask questions. Kind of a brand statement of sorts. Something that couldn’t be mistaken for a guitar you bought online. At the same time, working with Gen-Z there was no way this build could take months to complete, so we had to find a compromise, something we could make in just a few weekends. We agreed that designing a homemade body with a purchased neck would provide a good, playable instrument without needing the skills of a full-fledged luthier.
It was at this point that my job followed me home again and my 10-year-old became my latest client. These days there are a ton of computer assisted ways of creating designs and problem solving. With a sculptural form and no need for mass production, this seemed like a perfect excuse to go old school. I found myself sketching guitars, carving foam models, and rendering glitter paint as the deliverables for my “client”. Sometimes the process becomes just as important as the end result. In this case, by following the process we were able to produce a guitar that not only stood out on stage but made the “client” proud… as well as his dad!
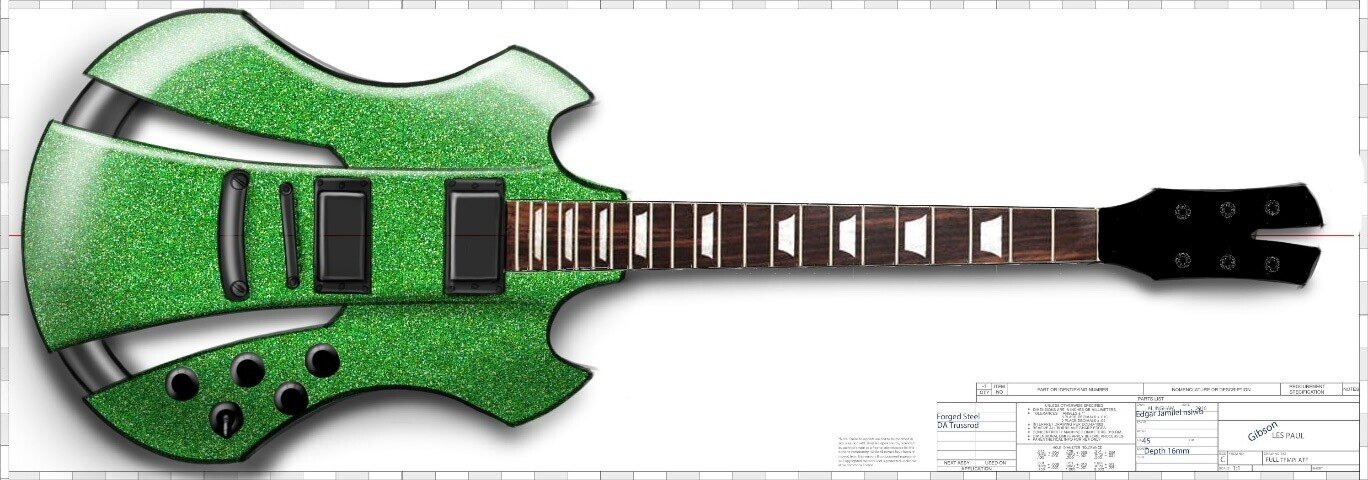
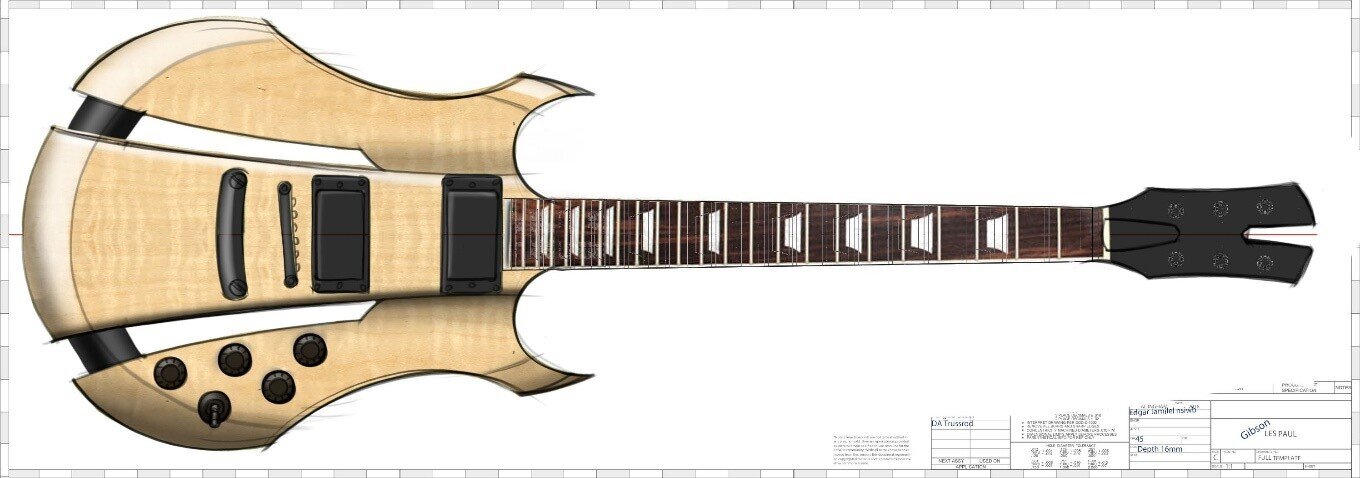
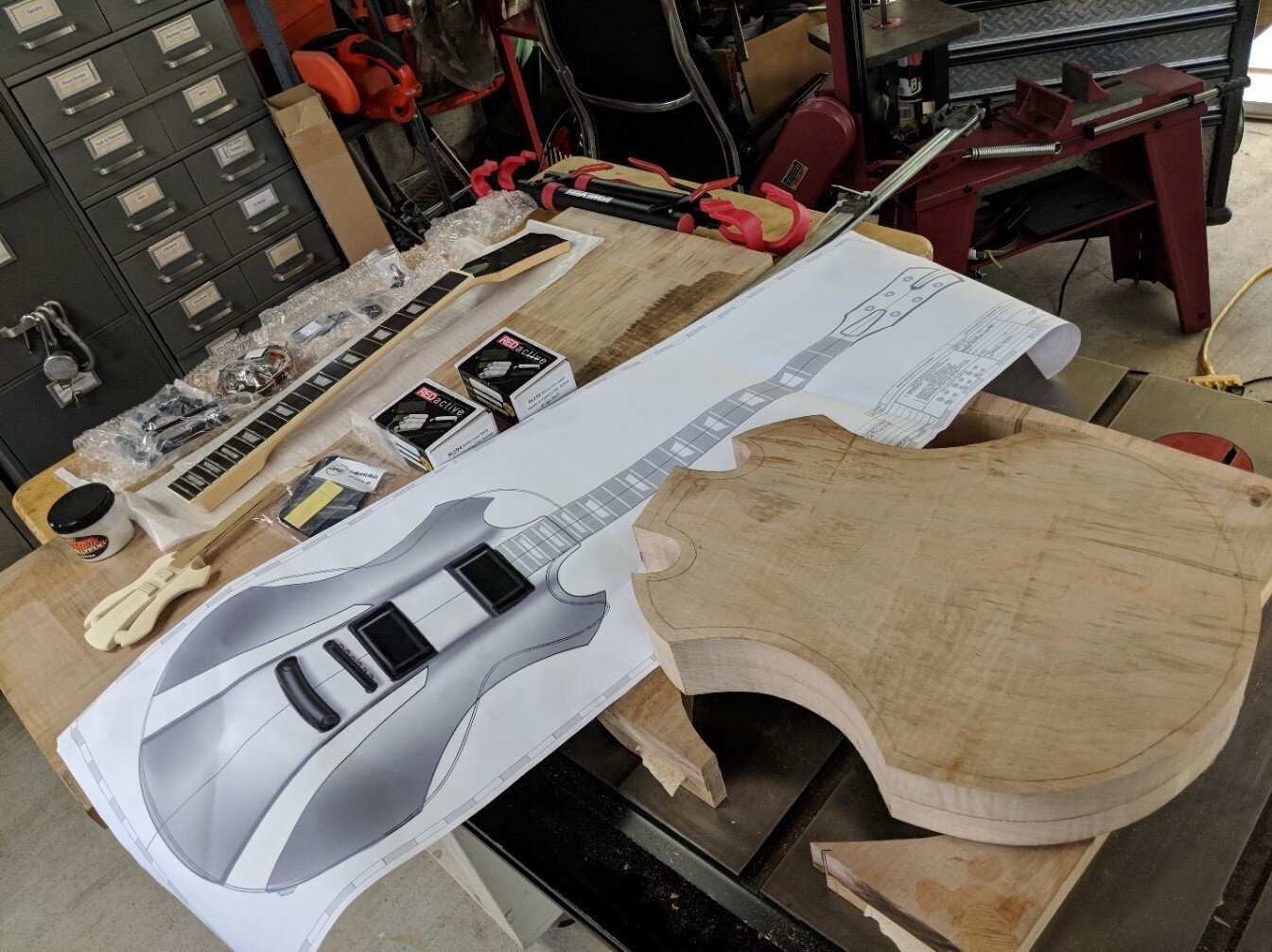
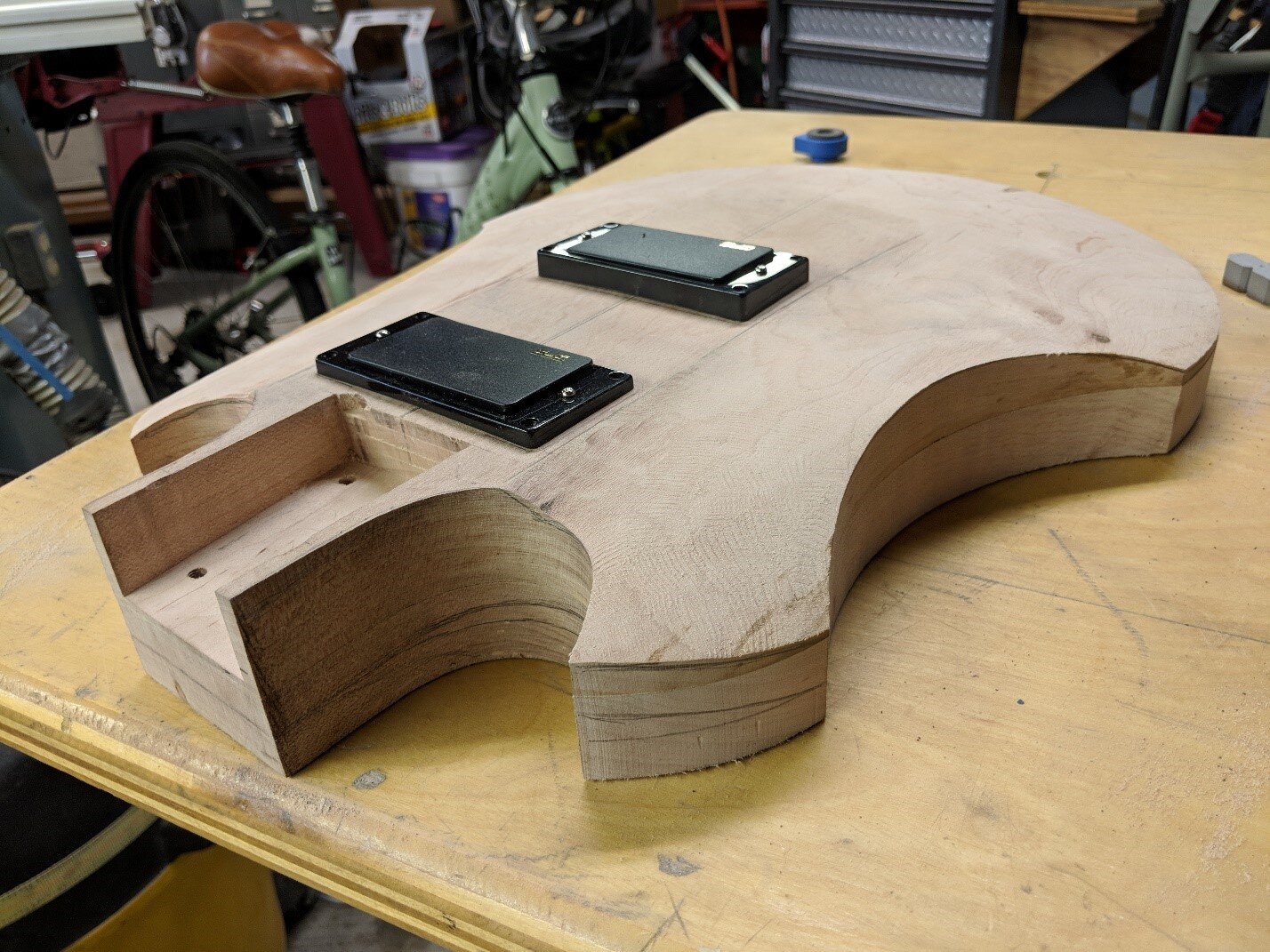
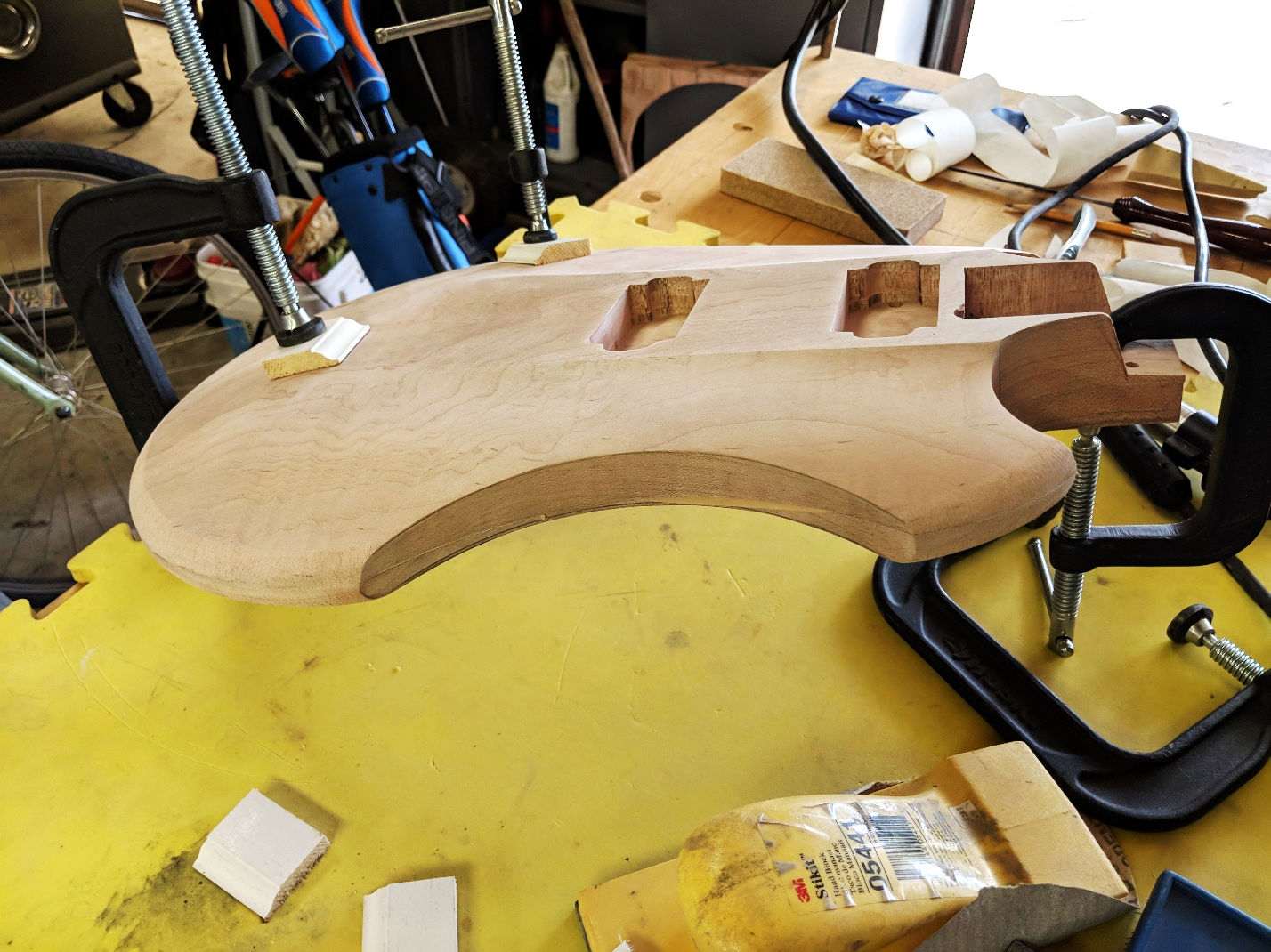
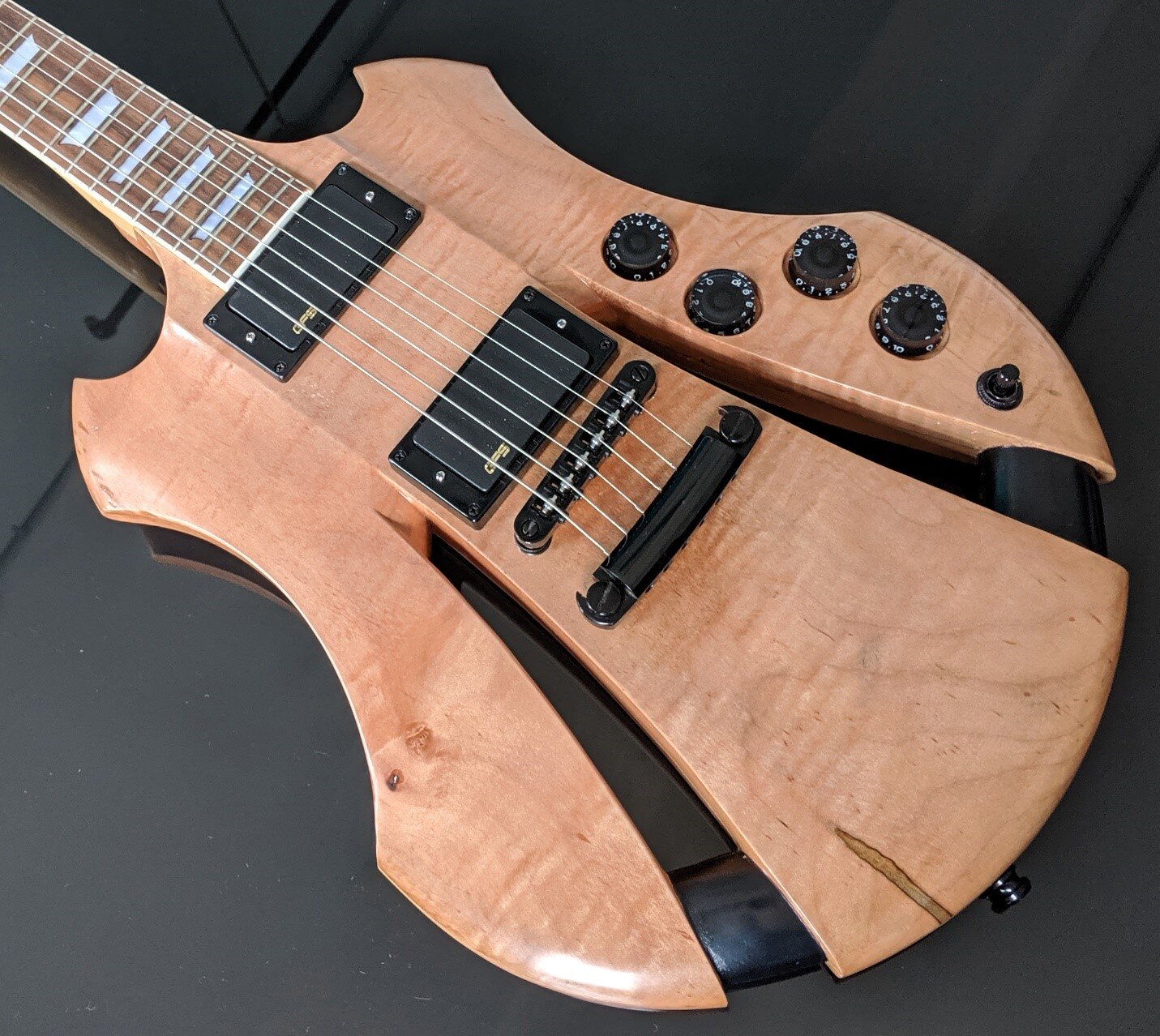
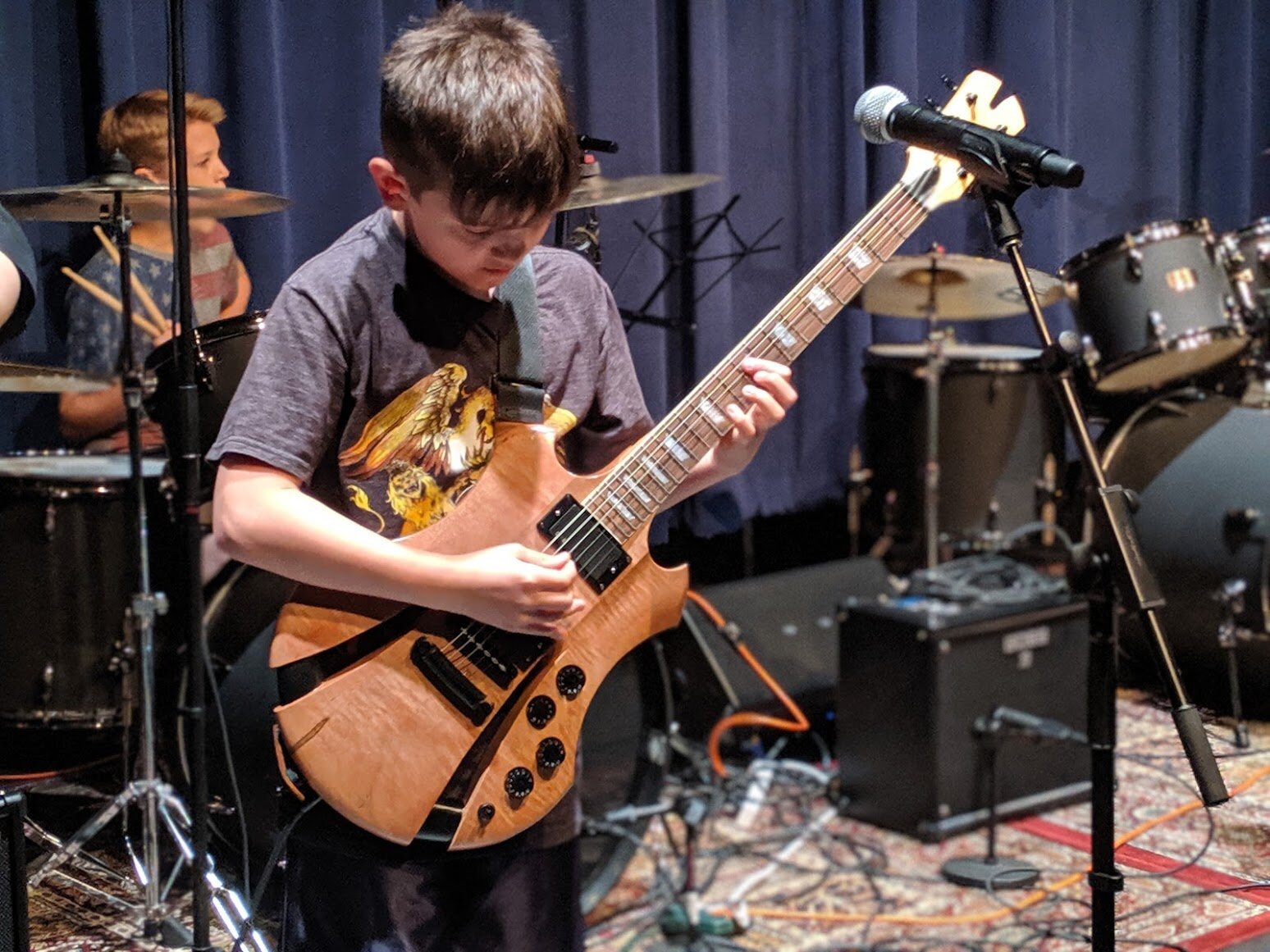